1. What is High Strength Worsted Yarns?
In the textile industry,
High Strength Worsted Yarns is a type of yarn with special properties and production processes. By definition, it is a yarn made of finer, longer and uniform high-quality wool as the main raw material using the worsted spinning process. During its production process, the combing process can effectively remove short fibers and impurities, so that the fibers in the yarn are arranged parallel and straight, and finally form a yarn with uniform and smooth strips.
-
The Key Factors of Raw Materials:
The fibers used in combed wool yarn are made of finer, longer and uniform high-quality wool as raw materials, which is one of the key factors that distinguishes it from other wool yarns. The characteristics of high-quality wool give the yarn an innate advantage. The finer fibers can make the yarn more delicate and soft to the touch; the longer fibers help to enhance the strength and stability of the yarn. When these high-quality wools are processed through a series of worsted spinning processes, high-strength combed wool yarns are born.
-
The Core of Production Process - Combing Process:
In the entire worsted spinning process, the combing process is particularly important. The combing process is like a strict screening process to remove short fibers and impurities that do not meet the requirements.
- In the pretreatment stage of raw wool, impurities, cotton seeds, etc. are first removed to ensure the cleanliness of the fibers;
- Then the fibers are preliminarily combed by carding (combing) to make them roughly straight;
- Then enter the combing stage, and use a combing machine to completely remove short fibers (usually <1 cm) and residual impurities, leaving only long and neat fibers;
- Finally, the combed fibers are processed by drawing and finally spun into uniform high-strength yarn.
-
The Distinctions from Ordinary Wool Yarn:
Compared with ordinary wool yarn, High Strength Worsted Yarns have obvious differences in many aspects. In the production process of ordinary wool yarn, the screening and combing of fibers are not as strict as those of combed wool yarn, so the fiber thickness of ordinary wool yarn may not be uniform, the short fiber content is relatively high, and there are more impurities. This results in the fact that ordinary wool yarn is far inferior to high-strength combed wool yarn in strength, and fabrics woven from ordinary wool yarn are prone to deformation and pilling. Fabrics made from high-strength combed wool yarn are more durable, have a high surface finish, are not easy to pilling, and have a delicate touch. For example, the quality and texture of worsted wool fabrics such as gabardine, valence, and palisade woven from high-strength combed wool yarn are far superior to similar products made from ordinary wool yarn.
2. What are the characteristics of High Strength Worsted Yarns?
The reason why High Strength Worsted Yarns occupies an important position in the textile field is inseparable from its unique characteristics. These characteristics cover multiple physical and chemical aspects, which not only determine the quality of the yarn itself, but also play a key role in its subsequent processing and the performance of the finished product.
(I) Physical properties
-
Strength:
The strength of High Strength Worsted Yarns is one of its most prominent physical properties. In the textile industry standards, the breaking strength of combed wool yarn is clearly stipulated, which should generally not be less than 28cN/tex. This value means that the yarn can withstand a large load without breaking when stretched by external force. High-strength combed wool yarn can have such high strength mainly due to its high-quality raw materials and special processing technology. High-quality wool fiber itself has high strength, and the combing process removes short fibers and impurities, making the fiber arrangement more compact and neat, greatly enhancing the overall strength of the yarn. In the production of some high-end suit fabrics, the use of high-strength combed wool yarn as raw material can ensure that the fabric is not easily damaged during daily wear and activities and is durable.
-
Abrasion resistance:
The wear resistance of this yarn is also excellent. Because the fibers are closely arranged and the yarn surface is relatively smooth, it is not easy to produce pilling and other phenomena when rubbing against other objects, which can effectively extend the service life of the fabric. Relevant studies have shown that the wear resistance of high-strength combed wool yarn is more than 30% higher than that of ordinary wool yarn. In practical applications, if high-strength combed wool yarn is used to make some fabrics such as work clothes and sofa covers that often rub against external objects, their wear resistance can be significantly improved, damage caused by friction can be reduced, replacement frequency can be reduced, and costs can be saved.
-
Stretching degree:
In terms of tensile properties, high-strength combed wool yarn has good elongation at break, which can usually reach a certain percentage. This allows the yarn to deform to a certain extent without breaking when subjected to tensile force, showing good flexibility and toughness. In the production of knitted products, the yarn needs to withstand a certain tensile force during the weaving process. The good stretching degree of high-strength combed wool yarn can ensure the smooth progress of the weaving process, while giving the knitted fabric good elasticity and comfort. Moreover, its stretch recovery performance is also good. When the external force is removed, it can basically return to its original length. This feature makes the fabric made of it not easy to deform during wearing.
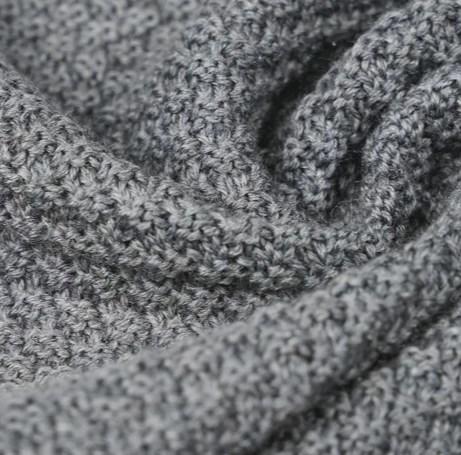
(II) Chemical properties
-
Chemical stability:
High Strength Worsted Yarns have good chemical stability. The chemical structure of wool fiber itself is relatively stable, and it is not easy to react chemically with other chemicals under general chemical conditions. Under normal washing and storage conditions, the color, strength and other properties of the yarn will not be significantly affected by chemical reactions. This allows clothing made of high-strength combed yarn to be washed in a variety of conventional ways, and consumers do not need to worry about the yarn being damaged by chemicals during the washing process, which greatly improves the practicality and durability of the product.
-
Corrosion resistance:
For some common chemical reagents, high-strength combed yarn shows a certain corrosion resistance. Although wool fiber is essentially a protein fiber and may be damaged in extreme chemical environments such as strong acids and alkalis, it can remain relatively stable and not easily corroded in weak acids, weak alkalis, and some chemical additives encountered in daily life and general industrial production. For example, in the printing and dyeing process of textiles, yarns will come into contact with various dyes and auxiliaries. High-strength combed yarn, with its corrosion resistance, can still maintain its own structure and performance integrity under the action of these chemicals, ensuring that the printed and dyed fabrics are bright in color and stable in quality.
3. The manufacturing process of High Strength Worsted Yarns is revealed
The manufacturing process of High Strength Worsted Yarns is a complex and delicate process, and each link plays a vital role in the final quality of the yarn. From the strict selection of raw materials to a series of processes such as combing, combing, spinning and post-processing, the textile industry contains advanced technologies and process know-how. The following will analyze these manufacturing process links in detail.
(I) Raw material selection
-
The Strict Selection of Wool:
The selection of raw materials is the first key link in the manufacture of high-strength combed wool yarn. Among the many fiber raw materials, wool is the main choice, especially high-quality fine wool. Merino wool, like Australia, is an ideal choice for the manufacture of high-strength combed wool yarn because of its slender, soft and high-strength fibers. The average diameter of this wool is usually between 19 and 21 microns, and the fiber length is generally around 60-100 mm, which can meet the strict requirements of high-strength combed wool yarn for raw material fineness and length.
-
The Scientific Blending of Chemical Fibers:
In addition to wool, chemical fibers also account for a certain proportion of the raw materials of high-strength combed wool yarn. For example, polyester fiber is often used in blending with wool due to its advantages such as high strength, wear resistance and wrinkle resistance. When blending, it is necessary to accurately control the proportion of chemical fiber added according to the specific needs of the product. If it is used to produce industrial textiles with extremely high requirements for wear resistance, the proportion of polyester fiber may be appropriately increased; if it is used to produce high-end clothing fabrics, in order to ensure good hand feel and wearing comfort, the content of chemical fiber will be relatively reduced, so that wool will occupy a dominant position in the blended raw materials.
-
The Strict Quality Inspection:
In actual production, wool of different varieties and origins, as well as different types of chemical fibers, have different properties. Therefore, textile companies need to conduct strict quality inspection and screening of various raw materials. The inspection items include fiber fineness, length, strength, curl, color and other indicators. Through these tests, it is ensured that the selected raw materials meet the production standards of high-strength combed wool yarn, laying a solid foundation for subsequent production processes.
(II) Combing and combing
-
The Key Role of Combing Process:
The combing and combing process is a key step to improve fiber quality and neatness. In the combing stage, the wool fibers that have been preliminarily treated are mainly combed with a combing machine. The working principle of the combing machine is to use various different specifications of card clothing to carefully comb the wool fibers, comb the entangled fibers into single fiber states, and remove impurities and short fibers from them. The combing process of the carding machine is divided into multiple stages, including pre-combing, main combing and final combing.
- In the pre-combing stage, the wool fibers are preliminarily combed with relatively coarse card cloth to untangle the fibers;
- In the main combing stage, finer card cloth is used to further comb the fibers to make them straighter;
- In the final combing stage, the fibers are finally combed and sorted to ensure that the combing effect of the fibers reaches the best state.
-
The Precision Control of Combing Process:
Although the wool fibers after combing have been preliminarily combed into single fiber states, they still contain a certain amount of short fibers and impurities, which requires further processing in the combing process. The combing process uses a combing machine to comb and screen the fibers more finely through key components such as the cylinder and top comb. When the combing machine is working, the combing needles on the cylinder will comb the fibers to remove short fibers and impurities; the top comb further combs the fibers to make the fibers more neat and parallel. During the combing process, various process parameters need to be strictly controlled, such as combing distance, cotton drop distance, cylinder positioning, etc.
- If the combing distance is too small, it may cause fiber damage; if it is too large, it will affect the combing effect and fail to effectively remove short fibers and impurities.
- The size of the cotton drop distance directly affects the combing cotton drop rate and combing quality, and needs to be reasonably adjusted according to the spinning line density and quality requirements.
- The positioning of the cylinder affects the movement coordination between the cylinder and the nipper and the separation roller, and plays an important role in the combing effect and the separation and joining of the fibers.
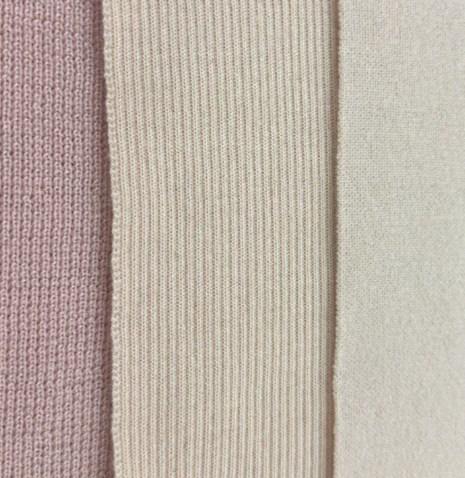
(III) Spinning process
-
Ring Spinning - The Mainstream Choice for High Quality:
The spinning process is the key link in spinning the combed and combed fibers into yarns. Different spinning methods have a significant impact on the quality of the yarn. Ring spinning is one of the most widely used spinning methods. In the ring spinning process, the fiber strips are stretched and thinned by the drafting device, and then twisted by the high-speed rotation of the wire ring on the steel collar, and finally wound into yarn. The advantages of ring spinning are that the yarn structure is compact, the strength is high, and the hairiness is relatively small. It is suitable for the production of various high-quality textiles, such as high-end clothing fabrics, home textile products, etc. When producing high-strength combed wool yarn, ring spinning can give full play to its advantages and make the strength and uniformity of the yarn reach a high level.
-
Air-jet Spinning - The Innovation with Efficiency:
Air-jet spinning is a new type of spinning method with a different working principle from ring spinning. Air-jet spinning uses a combing roller to comb the fiber strips into single fibers, and then uses air flow to transport the fibers to the spinning rotor, and twists them into yarn under the high-speed rotation of the spinning rotor. The characteristics of air-jet spinning are fast spinning speed and high production efficiency, which is suitable for the production of medium and low count yarns. However, compared with ring spinning, the yarn structure of air-jet spinning is relatively loose, the strength is slightly lower, and the hairiness is more. When producing high-strength combed wool yarn, air-jet spinning is generally rarely used alone. Instead, it will be combined with other spinning methods according to the special needs of the product to give full play to the advantages of various spinning methods.
-
The Diverse Choices of Spinning Methods:
In addition to ring spinning and air-jet spinning, there are other spinning methods such as air-jet spinning and vortex spinning. They each have unique spinning mechanisms and characteristics, and they also have certain applications in the production of high-strength combed wool yarn. Textile enterprises will comprehensively select appropriate spinning methods based on product quality requirements, production efficiency and cost factors to ensure that the high-strength combed wool yarn produced meets market demand.
(IV) Post-processing process
-
Twisting - The Key to Yarn Performance Optimization:
The post-processing process is an important link to improve the performance of High Strength Worsted Yarns, mainly including twisting, steaming and other processing processes. Twisting is one of the key steps in the post-processing process, which has an important impact on the strength, elasticity, feel and other properties of the yarn. Through twisting, the fibers in the yarn are entangled with each other, increasing the friction and cohesion between the fibers, thereby improving the strength of the yarn. However, the higher the degree of twisting, the better. When the twist exceeds a certain value, the strength of the yarn will decrease, and the feel will become harder and the elasticity will decrease. In actual production, it is necessary to reasonably control the degree of twisting according to the purpose and quality requirements of the yarn. For warp yarn, due to the need to withstand greater tension, the twist is usually appropriately increased to increase its strength; while weft yarn and knitting yarn pay more attention to softness and comfort, and the twist will be relatively small.
-
Steaming - The Secret to Yarn Performance Enhancement:
Steaming is also an indispensable part of the post-processing process. Yarn steaming is to steam and moisten the yarn with saturated steam. The purpose is to improve the breaking strength and breaking elongation of the yarn, reduce the yarn hairiness, maintain a uniform friction coefficient of cotton yarn, reduce the unwinding tension, stabilize the yarn twist, and thus improve the overall performance of the yarn. During the yarn steaming process, parameters such as steam temperature, pressure and treatment time need to be strictly controlled. For pure wool yarn, the recommended yarn steaming temperature is generally between 78 and 80 degrees Celsius, and the treatment time depends on the variety and specifications of the yarn, usually around 30 to 60 minutes. If the yarn steaming temperature is too high or the time is too long, the wool fiber may be damaged and the quality of the yarn may be affected; if the temperature is too low or the time is too short, the expected yarn steaming effect cannot be achieved.
-
The Comprehensive Enhancement of Post-treatment:
In addition to twisting and yarn steaming, the post-treatment process may also include sizing, softening and other links. These links work together to enable high-strength combed wool yarn to achieve ideal performance indicators and meet the needs of use in different fields.
IV. What are the application fields of High Strength Worsted Yarns?
Due to its outstanding characteristics, High Strength Worsted Yarns have extensive and important applications in many fields, from high-end clothing manufacturing to functional textiles to industrial uses, and they all play an irreplaceable role.
(I) High-end clothing manufacturing
In the field of high-end clothing manufacturing, High Strength Worsted Yarns is an ideal choice for making high-end clothing fabrics such as suits and dresses. In suit making, high-strength combed yarns show many advantages. Its high strength characteristics make suit fabrics more tough and durable. In daily wear and activities, it can withstand various external forces such as stretching and friction, and is not easy to break, which extends the service life of the suit. Suit fabrics woven with High Strength Worsted Yarns have high flatness, are crisp and stylish, and can well maintain the shape of the suit. When the wearer is active, the suit can naturally fit the body curve without wrinkles or deformation, showing the wearer's elegant temperament and professional image.
(II) Functional textiles
In the field of functional textiles, high-strength combed wool yarn is widely used in sports equipment and outdoor products. In terms of sports equipment, taking ski suits as an example, skiing has certain strength and risks, and ski suits need to have good wear resistance and windproof performance. Due to its own high strength and wear resistance, high-strength combed wool yarn can withstand the friction with objects such as snow and branches during skiing, and is not easy to be scratched or worn. At the same time, after special finishing processes such as waterproof and windproof treatment, ski suit fabrics made of high-strength combed wool yarn can effectively block the invasion of wind and snow, keeping the wearer's body dry and warm.
In the field of outdoor products, high-strength combed wool yarn also plays an important role. For example, tent fabrics. In the wild environment, tents need to withstand the test of various natural factors such as wind, sun, and rain. Tent fabrics made of high-strength combed wool yarn have high strength, can withstand certain wind pull, and are not easy to break; its good corrosion resistance and chemical stability enable it to maintain stable performance when facing erosion by rain, ultraviolet rays, etc., and extend the service life of the tent.
(III) Industrial Uses
In terms of industrial uses, high-strength combed wool yarn has unique application value in the fields of automotive interior and aerospace. In automotive interior, car seat fabrics need to have good properties such as wear resistance, comfort and flame retardancy. The high strength and wear resistance of high-strength combed wool yarn enable it to meet the frequent friction and extrusion of car seats in daily use
and are not easy to be damaged, which prolongs the service life of the seats. At the same time, its soft touch also provides passengers with a comfortable riding experience. Through post-finishing processes such as adding flame retardants, the seat fabrics made of high-strength combed wool yarn also have good flame retardant properties, which improves the safety of car interiors.
In the field of aerospace, the application of high-strength combed wool yarn has also gradually attracted attention. Aircraft interior materials need to have multiple properties such as light weight, high strength, fire resistance, and sound insulation. High-strength combed wool yarn can be compounded with high-performance materials such as carbon fiber to make lightweight and high-strength composite materials for aircraft seats, interior panels and other components. These composite materials can not only reduce the weight of the aircraft and reduce fuel consumption, but also improve the safety and comfort of the aircraft interior. During the flight of an aircraft, interior materials need to withstand various complex environmental factors. The chemical stability and corrosion resistance of high-strength combed wool yarn enable it to maintain stable performance in the harsh environment of high altitude, ensuring the quality and reliability of aircraft interiors.
V. Comparative analysis of high-strength combed wool yarn and other yarns
In the textile field, different types of yarns have their own characteristics. Compared with pure cotton yarn and chemical fiber yarn, high-strength combed wool yarn has obvious differences in many key aspects. These differences determine their applicability in different application scenarios.
(I) Comparison with pure cotton yarn
-
Strength: In terms of strength, high-strength combed wool yarn has significant advantages. The strength of pure cotton yarn is relatively low, and its breaking strength is generally 20-25cN/tex. This is because the length of cotton fibers is relatively short and the cohesion between fibers is weak. High-strength combed wool yarn uses high-quality wool raw materials and is processed by special processes such as combing. The fibers are arranged tightly and neatly, and its breaking strength is usually not less than 28cN/tex, which can withstand greater external force stretching. In industrial textiles, such as conveyor belts and ropes that need to withstand large tensile forces, if pure cotton yarn is used, it is easy to break during use due to insufficient strength, affecting the normal use and safety of the product; high-strength combed wool yarn can meet these application scenarios with high strength requirements and ensure the quality and reliability of the product.
-
Hygroscopicity: Pure cotton yarn is known for its excellent hygroscopicity. Under standard atmospheric conditions, the moisture regain of pure cotton yarn can reach 8-10%, which makes pure cotton fabrics very comfortable to wear and can quickly absorb sweat from the human body surface to keep the skin dry. In contrast, the hygroscopicity of high-strength combed wool yarn is slightly inferior, and its moisture regain is generally 14-16%. However, the hygroscopicity of wool fiber is also unique. It can absorb a lot of water while still maintaining a dry feel, which is not available in pure cotton yarn. In the hot and sweaty environment of summer, pure cotton T-shirts can quickly absorb sweat, making people feel refreshed and comfortable; in a relatively humid environment, although the moisture absorption of clothes made of high-strength combed wool yarn is not as good as that of pure cotton, it can evenly distribute the absorbed moisture on the fiber surface and will not make people feel sticky.
-
Abrasion resistance: In terms of abrasion resistance, high-strength combed wool yarn performs better. Pure cotton yarn is prone to pilling after repeated friction. This is because the wear resistance of cotton fiber is relatively poor, and the fiber is easy to break and entangle during the friction process. Relevant experimental data show that under the same friction conditions, the degree of wear of pure cotton yarn is significantly higher than that of high-strength combed wool yarn. The fibers of high-strength combed wool yarn are closely arranged and the surface is smooth, which can effectively resist friction and reduce the occurrence of pilling and pilling. For some work clothes and gloves that often rub against external objects, if they are made of pure cotton yarn, the service life will be short and need to be replaced frequently; while using high-strength combed wool yarn can greatly improve the wear resistance of the product, extend the service life, and reduce the cost of use.
(II) Comparison with chemical fiber yarns
-
Cost: From a cost perspective, chemical fiber yarns have certain advantages. The raw materials of chemical fiber yarns mainly come from petroleum and other chemical products. The production process is relatively simple and the scale of production is high, so the cost is relatively low. For example, the common polyester fiber yarn is usually more affordable. The raw material of high-strength combed wool yarn is mainly high-quality wool. The breeding and collection costs of wool are high, and the production process is complex, requiring multiple fine processes, resulting in relatively high costs. In the large-scale production of ordinary textiles that are more sensitive to costs, chemical fiber yarns are more cost-competitive; but for some products with extremely high quality requirements and the pursuit of high-end quality, such as high-end clothing and luxury goods, consumers are relatively less sensitive to prices and pay more attention to the quality and uniqueness of the products. High-strength combed wool yarn still occupies an important position in these fields with its excellent performance.
-
Functionality: In terms of functionality, both have their own advantages. Chemical fiber yarn has many unique functional properties, such as polyester fiber yarn has good wrinkle resistance, abrasion resistance and quick drying, and nylon fiber yarn has excellent abrasion resistance and strength. However, high-strength combed wool yarn also has its irreplaceable functionality. It has natural warmth retention. There are many air chambers inside the wool fiber, which can store a lot of air. Air is a poor conductor of heat, which makes the clothing made of high-strength combed wool yarn have excellent warmth retention performance. Its good air permeability and moisture absorption can adjust the humidity balance between the human body and the external environment, making people more comfortable to wear. In the cold winter, warm clothing such as sweaters and scarves made of high-strength combed wool yarn can effectively resist the severe cold; in the field of sportswear, although chemical fiber yarn has certain advantages in quick drying, the air permeability and moisture absorption of high-strength combed wool yarn can also meet the athletes' needs for comfort during exercise, and its natural fiber characteristics are less irritating to the skin.
-
Environmental protection: In terms of environmental protection, high-strength combed wool yarn has obvious advantages. Wool is a natural fiber that is biodegradable and can be decomposed by microorganisms in the natural environment without causing long-term pollution to the environment. However, most chemical fiber yarns are made of chemical synthetic materials and are difficult to degrade naturally. After being discarded, they will remain in the environment for a long time, causing pollution to soil, water sources, etc. As people's environmental awareness continues to improve, environmental protection requirements for textiles are becoming increasingly stringent. Under the general trend of sustainable development, high-strength combed wool yarn, as an environmentally friendly yarn, is more in line with the development needs of the times and has broad application prospects in the environmentally friendly textile market. Some brands that pursue environmental protection concepts will give priority to high-strength combed wool yarn as raw materials in product research and development to meet consumers' demand for environmentally friendly products and enhance their brand image.
VI. What is the market prospect of high-strength combed wool yarn?
(I) Market demand trend
With the development of the global economy and the improvement of people's living standards, consumers' demand for high-quality textiles has shown a significant growth trend, which has brought broad development opportunities to the high-strength combed wool yarn market. In the field of clothing, consumers have a higher pursuit of clothing quality, comfort and fashion sense. High-strength combed wool yarn has become an ideal raw material for making high-end clothing due to its excellent properties, such as soft feel, excellent warmth retention, good breathability, and resistance to pilling and deformation. In the high-end men's clothing market, suits made of high-strength combed wool yarn are not only comfortable to wear, but also can show the wearer's elegant temperament and taste. They are deeply loved by business people and successful people, and the market demand continues to grow. As people pay more attention to the quality of life, the requirements for home textiles are also increasing. High-strength combed wool yarn can be used to make high-end bedding, curtains, carpets, etc. These products not only have beautiful and generous appearance, but also can add a warm and comfortable atmosphere to the home environment, satisfying consumers' pursuit of high-quality life, and the market prospects are very broad.
(II) Industry competition pattern
In the high-strength combed wool yarn industry, there are many domestic and foreign production enterprises, and the competition situation is relatively fierce. Some well-known foreign companies, relying on advanced technology, rich experience and high-quality brand image, occupy an important position in the high-end market. Some wool spinning companies in Italy have a long history and exquisite craftsmanship. The high-strength combed wool yarn they produce is sold well in the global high-end clothing market with its excellent quality and unique design, and has become the preferred supplier of many international first-line brands. Domestic wool spinning companies have also developed rapidly in recent years, and have achieved remarkable results in technological innovation, product quality improvement and brand building. Domestic large-scale wool spinning companies not only occupy a large share of the domestic market, but also actively expand the international market. By introducing advanced production equipment and technology, they continuously improve product quality and production efficiency, and compete strongly with foreign companies. Some small and medium-sized wool spinning companies focus on specific market segments through differentiated competition strategies, produce high-strength combed wool yarn products with characteristics, meet the personalized needs of different customers, and also occupy a place in the market.
(III) Development Challenges and Opportunities
The high-strength combed wool yarn industry has faced both challenges and opportunities in its development process. Fluctuations in raw material prices are a major challenge facing the industry. The price of wool, the main raw material for high-strength combed wool yarn, is affected by a variety of factors such as breeding costs, climatic conditions, and market supply and demand, and fluctuates greatly. If the price of wool rises sharply, it will directly increase the production cost of enterprises, compress profit margins, and bring pressure to the production and operation of enterprises. The pressure of technological innovation is also a major challenge for the development of the industry. With the continuous improvement of consumers' requirements for product quality and performance, and the increasingly fierce market competition, enterprises need to continuously increase their investment in technological innovation and develop higher-quality and more distinctive high-strength combed wool yarn products. This requires enterprises to have strong R&D capabilities and financial strength. For some small and medium-sized enterprises, technological innovation is more difficult.
However, the industry has also ushered in many development opportunities. With the continuous enhancement of environmental awareness, consumers' demand for environmentally friendly textiles has gradually increased. As a natural fiber product, high-strength combed wool yarn has the advantages of biodegradability and environmental protection, which meets the market demand trend for environmentally friendly products, which provides new opportunities for the development of the industry. Some companies have further improved the environmental performance of high-strength combed wool yarn by developing environmentally friendly production processes and finishing technologies, which has been favored by the market. The promotion of the "Belt and Road" initiative provides a good opportunity for the high-strength combed wool yarn industry to expand the international market. Countries and regions along the route have a large demand for textiles. China's wool spinning enterprises can take advantage of this opportunity to strengthen trade cooperation with countries and regions along the route, expand product exports, and increase international market share. Technological innovation has also brought opportunities for the development of the industry. With the application of intelligent and automated technologies in the textile industry, enterprises can improve production efficiency, reduce production costs, improve product quality, and enhance market competitiveness. Some companies have introduced intelligent spinning equipment to achieve precise control and automated operation of the production process, which not only improves production efficiency, but also reduces the impact of human factors on product quality, and the quality of high-strength combed wool yarn produced is more stable.
VII. What is the future development direction of high-strength combed wool yarn?
(I) Technological innovation trend
-
The Breakthrough of New Spinning Technology:
From the perspective of spinning technology, the continuous emergence of new spinning technologies will bring new opportunities for the development of high-strength combed wool yarn. Compact spinning technology has developed rapidly in recent years. It reduces the loss of fibers and the generation of hairiness by compactly agglomerating fibers during the spinning process, making the yarn structure more compact and significantly improving strength. In the compact spinning process, the fibers are tightly gathered together under the action of the gathering device to form a more uniform and compact yarn structure, which not only improves the strength of the yarn, but also improves the appearance quality of the yarn, making it smoother and smoother. Compact spinning technology can also reduce the hairiness content of the yarn, reduce the difficulty of subsequent processing caused by hairiness problems, and improve production efficiency and product quality. In the knitting and weaving process, yarns with less hairiness can reduce the occurrence of broken ends and defects, and improve the quality and production efficiency of the fabric.
-
The Frontier of Fiber Modification Technology:
In terms of fiber modification technology, the performance of high-strength combed yarn can be further improved by physically or chemically modifying wool fibers. The surface modification of wool fibers using plasma treatment technology can improve the surface properties of the fibers, increase the cohesion between the fibers, and thus enhance the strength of the yarn. Plasma treatment can introduce active groups on the surface of wool fibers, increase the roughness of the fiber surface, increase the friction between the fibers, and enhance the cohesion. In this way, during the spinning process, the fibers can better combine with each other to form a more solid yarn structure, which improves the strength and stability of the yarn. By introducing functional groups into wool fibers through chemical grafting, special functions such as antibacterial and UV protection can be given to the yarn. In some high-end sportswear and outdoor products, the fabrics need to have antibacterial and UV protection functions. By chemically grafting wool fibers, high-strength combed yarns can have these special functions to meet the market demand for functional textiles.
(II) Environmentally friendly and sustainable development
-
The Practice of Energy Conservation in Production:
In the production process, reducing energy consumption is one of the important goals of achieving environmentally friendly and sustainable development. Textile enterprises can reduce energy consumption by adopting high-efficiency and energy-saving equipment. New spinning equipment uses advanced motor technology and transmission system, which can improve energy utilization efficiency and reduce energy consumption per unit output. Some enterprises have introduced variable frequency speed regulation technology to automatically adjust the speed of the equipment according to the needs of the production process, avoiding the waste of energy when the equipment is running at unnecessary high speed. Optimizing the production process can also reduce energy consumption. By reasonably arranging the production process, reducing the idle time of the equipment, improving production efficiency, and thus reducing energy consumption. In the combing and combing process, the operating parameters of the equipment are accurately controlled to ensure that energy waste is minimized while ensuring product quality.
-
The Commitment to Pollution Reduction:
Reducing environmental pollution is also the key to environmentally friendly and sustainable development. In terms of wastewater treatment, textile enterprises can adopt advanced sewage treatment technology to effectively treat and recycle wastewater generated during the production process. Some enterprises have adopted a combination of biological treatment and membrane separation technology, which can effectively remove pollutants from wastewater, so that the treated wastewater meets the discharge standards and can even be reused in some links of the production process, realizing the recycling of water resources and reducing the waste of water resources and pollution to the environment. In terms of waste gas treatment, the installation of efficient dust removal equipment and waste gas purification devices can effectively reduce the pollution of the atmospheric environment by waste gas generated in the production process. For the dust generated in the combing and spinning process, it is collected and treated by efficient dust removal equipment to avoid dust emission into the atmosphere; for the harmful gases generated in the dyeing and finishing process, the waste gas purification device is used to treat it, reduce the emission concentration of harmful gases, and protect the atmospheric environment.
VIII. Conclusion
High-strength combed wool yarn occupies an indispensable position in the textile field due to its excellent performance. From high-end clothing to functional textiles to industrial uses, it is everywhere, providing strong support for people's lives and the development of many industries. With the continuous innovation of technology, new spinning technology and fiber modification technology will further improve its performance and expand its application areas. Under the general trend of environmental protection and sustainable development, the high-strength combed wool yarn industry is also actively exploring ways to reduce energy consumption and pollution to achieve green development. In the future, as market demand continues to change, high-strength combed wool yarn will develop in the direction of product diversification to meet the needs of different fields and different consumers. It can be foreseen that high-strength combed wool yarn will continue to play an important role in the future textile market and usher in a broader development space.